ABS (Acrylonitrile Butadiene Styrene) is a widely used thermoplastic known for its high impact resistance, manufacturing flexibility, and cost-effectiveness. From household appliances to automotive components, ABS is a top choice in industrial and consumer applications due to its balanced properties.
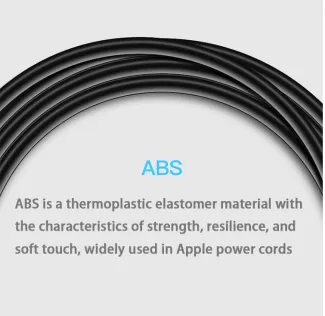
Basic Properties
- High Impact Resistance
Butadiene enhances ABS’s ability to withstand physical shocks, ideal for high-impact environments. - Heat Resistance
Short-term heat tolerance of 80–100°C, suitable for most daily applications. - Ease of Processing
Easily molded via injection or extrusion; surfaces can be painted or electroplated. - Lightweight & Rigid
Low density (~1.05g/cm³) with strong mechanical performance.
Key Applications
- Consumer Electronics
Keyboards, printer casings, game controllers (e.g., LEGO bricks). - Automotive
Dashboards, interior trim, grille components. - Home Appliances
Vacuum cleaner housings, coffee maker parts, toys. - Industrial Equipment
Pipe fittings, tool handles, protective covers.
Pros & Cons
Pros:
- Low cost, ideal for mass production.
- High-gloss finish, easy to post-process (e.g., painting, laser engraving).
- Resistant to oils and weak acids.
Cons:
- Poor UV resistance; yellows under prolonged sunlight.
- May release trace styrene vapors at high temperatures.
Safety & Sustainability
- Safety Certifications
Compliant with RoHS and REACH standards, restricting hazardous substances (e.g., lead, cadmium). - Recycling
ABS is mechanically recyclable but requires separation from other plastics like PC. - Innovations
Bio-based ABS (e.g., sugarcane-derived variants) aims to reduce carbon footprint.
Future Trends
- High-Performance Blends
ABS-PC alloys for enhanced heat resistance and strength. - Smart Modifications
UV stabilizers or conductive fillers for outdoor/electronics use. - Circular Economy
Closed-loop recycling systems to improve recycled ABS quality.